Метод за алкилиране на бензен с етилен
Собственици на патент RU 2261853:
Употреба: рафиниране на нефт и нефтохимия. Същност: реакциите на алкилиране и трансалкилиране се извършват в един етап чрез зареждане на смес от два различни катализатора в един реактор: EBEMAX-1 катализатор за алкилиране и EBEMAX-2 катализатор за трансалкилиране. Съотношение на масата на катализаторите (20-1):1, съответно. Процесът се провежда при 380-450°C. Технологичен резултат: увеличаване на добива на етилбензол и селективността на процеса на алкилиране при намаляване на енергоемкостта и оперативните разходи на процеса на алкилиране на бензен с етилен. 1 табл.
Изобретението се отнася до получаването на етилбензен чрез каталитично алкилиране на бензен с етилен.
Известен е метод за получаване на етилбензен чрез взаимодействие на бензен с етилен при температура 100-250°C и моларно съотношение бензен:етилен (3÷10):1 в присъствието на киселинен зеолит-съдържащ катализатор (US патент No. 4849570, клас C 07 C 02/68).
Най-близък по техническа същност и постигнат резултат до предложеното изобретение е метод за алкилиране на бензен с етилен и трансалкилиране на диетилбензени (Технологичен регламент за производство на етилбензол на цех № 46 на АО "Салаватнефтеоргсинтез" - прототип).
Съгласно прототипа, алкилирането на бензен с етилен и трансалкилирането на диетилбензени се извършва съгласно следните реакции.
Основната реакция на алкилиране на бензен с етилен, която протича в реактора за алкилиране на зеолитния катализатор, е реакцията между бензен и етилен с образуването на етилбензен
В допълнение към основната реакция в реактора за алкилиране протичат странични реакции както с участието на основната суровина, така и с участието на примеси, съдържащи се в суровината. Етилбензенът се алкилира до образуванедиетилбензени и триетилбензени

В резултат на разрушаването на алкиловите групи по време на алкилирането се образуват ксилени
Необходимият за това водород се образува чрез реакцията на дехидрокондензация на ароматни съединения, което води до смолисти вещества, обеднени на водород (реакции на коксуване).
Основните продукти на превръщането на толуена - примеси в пресния бензен - са ксилен и бензен
В реактора за трансалкилиране, в резултат на реакцията на трансалкилиране (междумолекулна миграция на алкилови групи между бензен и диетилбензен), се образува етилбензен
Описание на технологичната схема
Алкилиране на бензен с етилен
Бензолов заряд-1, масовата част на бензена, в която е не по-малка от 98,0%, се нагрява от 155-160 ° C до 233-242 ° C поради топлината на алкилат-1. След това заряд-1 се подава в два потока за изпарение и прегряване. Основният поток от заряд-1 с температура на парите 380-425°C се изпраща към първата секция на реактора за алкилиране.
Реакторът за алкилиране се състои от шест секции, всяка от които съдържа слой катализатор.
Вторият поток - "студен" заряд-1 с температура на парите 260-280°C се изпраща в секцията на реактора за алкилиране за охлаждане на вътрешните технологични потоци.
Етиленът се подава към тръбопровода на основния поток заряд-1 на входа на реактора за алкилиране и към "студения" поток във всяка секция. В реактора в присъствието на зеолит-съдържащ катализатор EVEMAX-1, следният химичен състав: SiO2 69.0; Al2O3 30,97; N2O 0,03 тегл.%, съответно, реакцията на алкилиране на бензен с етилен протича при температура 380-425 ° C и налягане 17-24 atm.
Процесът на алкилиране е екзотермичен. Извършва се намаляване на температурата на потока на входа на всяка следваща секция на реактора"студен" поток от заряд-1.
Температурата във всяка секция на реактора, налягането на входа и изхода на реактора и спадът на налягането в реактора се контролират.
Процес на трансалкилиране на диетилбензени до етилбензен
Процесът на трансалкилиране се извършва в реактор. Диетилбензените в смес с обратен бензен - заряд-2 се нагряват от 80-90°C до 240-250°C поради топлината на алкилат-2. След това заряд-2 влиза в пещта за изпаряване и прегряване. От пещта двойка заряд-2 с температура 420-460°C влиза в реактора за трансалкилиране.
В реактора в присъствието на зеолит-съдържащ катализатор за трансалкилиране EBEMAX-2, следният химичен състав: SiO2 72.0; Al2O3 27,94; N2O 0,06 тегл.%, съответно реакцията на трансалкилиране-реалкилиране на диетилбензени в етилбензен протича при температура 420-460°C и налягане 17-24 atm.
Реакторът за трансалкилиране се състои от 3 секции, съдържащи каталитични слоеве. Контролират се температурата във всяка секция на реактора, както и налягането на входа и изхода на реактора, както и спадът на налягането в реактора.
Както показва проучването на работата на цех № 46 за производство на етилбензол по горната технология в АД Salavatnefteorgsintez, добивът на етилбензол в процеса на трансалкилиране на диетилбензени в етилбензен е много нисък. В същото време селективността на процеса на алкилиране на бензен с етилен е недостатъчна.
Целта на изобретението е да се увеличи добивът на етилбензен и селективността на комбинирания процес на алкилиране-трансалкилиране при намаляване на потреблението на енергия и експлоатационните разходи.
Тази цел се постига чрез едновременно провеждане на процесите на алкилиране и трансалкилиране чрез зареждане на бензен в един и същ реактор за алкилиранеетиленът е смес от два различни типа катализатори, а именно катализатори за алкилиране и трансалкилиране. В този случай масовото съотношение на катализаторите в сместа (20÷1):1, респ. Процесът се провежда при температура 380-450°C.
Сравнителният анализ на предложения метод с прототипа ни позволява да заключим, че предложеният метод се различава от известния с това, че в един реактор - алкилатор се използва едновременно смес от различни зеолит-съдържащи катализатори (EVEMAX-1 алкилиране и EVEMAX-2 трансалкилиране). Съотношението на масата на катализаторите в сместа (20÷1):1, респ. Температурата на процеса на алкилиране е 380-450°C.
Тази техника ни позволява да заключим, че предложеното техническо решение отговаря на критерия "новост".
Анализ на известните методи за алкилиране на бензен с етилен и трансалкилиране на диетилбензени до етилбензен показа, че е известно използването на катализатори за алкилиране и трансалкилиране за производството на етилбензен. Фактът за провеждане на реакции при температури от 380-425 ° C също е известен. Но само фактът на зареждане на смес от катализатори за алкилиране и трансалкилиране в един реактор при масово съотношение на катализаторите в сместа (20÷1): 1, съответно, и осъществяването на процеса в един етап при температура 380-450 ° C позволява да се увеличи добивът на етилбензен, да се подобри селективността на комбинирания процес, като същевременно се намалят консумацията на енергия и експлоатационните разходи.
Същността на изобретението е както следва и се осъществява съгласно следните реакции.
Основната реакция на алкилиране на бензен с етилен, която протича в реактора за алкилиране върху зеолитен катализатор, е реакцията между бензен и етилен с образуването на етилбензен
В допълнение към основната реакция в реактора за алкилиранестраничните реакции протичат както с участието на основната суровина, така и с участието на съдържащите се в суровината примеси. Етилбензенът се алкилира до диетилбензени и триетилбензени
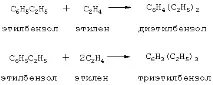
В резултат на разрушаването на алкиловите групи по време на алкилирането се образуват ксилени
Необходимият за това водород се образува от реакцията на дехидрокондензация на ароматни съединения, което води до смолисти вещества, обеднени на водород (реакции на коксуване).
Основните продукти на превръщането на толуена - примеси в пресния бензен - са ксилен и бензен
В същото време етилбензенът се образува в реактора в резултат на реакцията на трансалкилиране (трансалкилиране, междумолекулна миграция на алкилови групи между бензен и диетилбензен).
Описание на технологичната схема
Бензеновата смес се нагрява от 155-160°C до 233-242°C поради топлината на алкилата. След това зарядът се подава в два потока за изпаряване и прегряване. Основният поток от сместа с температура на парите 380-450 ° C се насочва към първата секция на реактора.
Реакторът се състои от 6 секции, всяка от които съдържа слой от смес от катализатори. Катализаторите EVEMAX-1 за алкилиране и EVEMAX-2 за трансалкилиране-реалкилиране се смесват предварително преди зареждане в масово съотношение на катализаторите в смес (20÷1):1 съответно и се разпределят равномерно в 6 секции на реактора.
Вторият поток - "студен" заряд с температура на парите 260-280 ° C се изпраща в секцията на реактора за охлаждане на вътрешните технологични потоци.
Етиленът се подава към тръбопровода на основния заряден поток на входа на реактора и към "студения" поток във всяка секция.
Реакциите на алкилиране на бензен с етилен итрансалкилиране-реалкилиране на диетилбензени (междумолекулна миграция на алкилови групи между бензен и диетилбензен) при температура 380-450°C и налягане 17-24 atm.
Процесът е екзотермичен. Намаляването на температурата на потока на входа на всяка следваща секция на реактора се осъществява от "студения" заряден поток.
Температурата във всяка секция на реактора, налягането на входа и изхода на реактора и спадът на налягането в реактора се контролират.
Зареждането в един и същ реактор на смес от два различни катализатора: катализатор за алкилиране и трансалкилиране прави възможно пълното решаване на проблема с алкилирането на бензен и трансалкилирането-реалкилирането на диетилбензени в един и същ реактор. Не е необходимо да се използва единица за трансалкилиране, която е изведена от експлоатация. Във връзка с гореизложеното АО "Салаватнефтеоргсинтез" постигна значително увеличение на добива на етилбензол и подобряване на селективността на процеса при намаляване на потреблението на енергия и оперативните разходи.
Бензеновата смес се нагрява от 155-160°C до 233-242°C поради топлината на алкилата. След това зарядът се подава в два потока за изпаряване и прегряване. Основният поток от сместа с температура на парите 380°C се насочва към първата секция на реактора.
Реакторът се състои от шест секции, всяка от които съдържа слой от смес от EBEMAX-1 алкилиращи и EBEMAX-2 катализатори за трансалкилиране-реалкилиране. Масовото съотношение на катализаторите в сместа е 1:1.
Вторият поток - "студен" заряд с температура на парите 260-280 ° C се изпраща в секцията на реактора за охлаждане на вътрешните технологични потоци.
Етиленът се подава към тръбопровода на основния заряден поток на входа на реактора и към "студения" поток във всяка секция.
В реактора в присъствието на смес от зеолит-съдържащакатализатори EVEMAX-1, 2 протичат реакцията на алкилиране на бензен с етилен и трансалкилиране-реалкилиране на диетилбензени при температура 380 ° C и налягане 17 atm.
Влиянието на условията на комбинирания процес на алкилиране-трансалкилиране върху въглеводородния състав на реакционните продукти и добива на етилбензен на преминал бензен (селективност) са показани в таблицата.
Данните от други примери също са представени в таблицата.