Присвояване на намесата
Интерферентните кацания са предназначени за неподвижни, еднокомпонентни (или разглобени само в някои случаи по време на ремонт) съединения на части, като правило, без допълнително закрепване с винтове, щифтове, ключове и др. Относителната неподвижност на частите по време на тези кацания се постига поради напрежения, възникващи в материала на свързващите се части поради действието на деформации на техните контактни повърхности. При равни други условия напреженията са пропорционални на плътността. В повечето случаи интерферентните съединения причиняват еластични деформации на контактните повърхности, но при редица интерферентни съвпадения, особено при относително големи намеси или в ставите на части от леки сплави и пластмаси, възникват еластопластични деформации (пластичните деформации в едната или двете части не се простират до цялата дебелина на материала) или пластични деформации, които се простират до цялата дебелина на материала. Използването на такива площадки в много случаи е възможно и целесъобразно.
За разлика от други методи за осигуряване на неподвижност на частите във връзката по време на прехвърляне на товари, намесата ви позволява да опростите дизайна и сглобяването на части и да осигурите висока степен на центриране. В сравнително редки случаи, при предаване на много големи въртящи моменти или при наличие на много големи срязващи сили, крепежните елементи се използват допълнително в интерферентни връзки.
При същото напрежение силата на връзката зависи от материала и размерите на частите, грапавостта на свързващите повърхности, метода на свързване на частите, формата и размера на центриращите фаски, скоростта на смазване и пресоване, условията на нагряване или охлаждане и др. С оглед на такова разнообразие от първоначални фактори, изборът на кацане трябва да се прави не само по аналогия с известни съединения, но ивъз основа на предварителни изчисления на напрежението и възникващите напрежения, особено при използване на сглобки с относително големи намеси. За продукти от серийно и масово производство се препоръчва да се извърши предварителна експериментална проверка на избраните намеси.
Има следните основни методи за сглобяване на части по време на намесата:
1) Сглобяване под налягане поради аксиална сила при нормална температура, така нареченото надлъжно пресоване;
2) Сглобяване с предварително нагряване на женската част (отвор) или охлаждане на мъжката част (вал) до определена температура (метод на термична деформация или напречно пресоване).
Във всеки конкретен случай изборът на метод на сглобяване се определя от конструктивни съображения (форма и размери на свързващите части, стойности на смущения, наличие на подходящо оборудване за сглобяване и др.).
Сглобяването под налягане е най-добре познатият и прост процес, използван главно с относително малка намеса (до 0,001 dn.s.). Неговите недостатъци обаче включват: неравномерна деформация на тънкостенни части, възможност за повреда на чифтосващи се части, необходимост от мощни преси, по-високи изисквания за грапавостта на чифтосващите се повърхности.
Сглобяването по метода на термичните деформации се използва както при относително големи, така и при малки смущения и дава по-високо качество на връзката поради по-малко увреждане на свързващите части и намаляване на ефекта на грапавостта на повърхността.
1.2 Изчисляване на намесата.
Изчисляването на смущенията се извършва, за да се осигури здравината на връзката, т.е. липса на премествания на свързващите се части под действието на външни натоварвания и здравината на свързващите се части. Въз основа на първото условие,определя се минимално допустимата плътност [Nmin], µm, необходима за възприемане и предаване на външни натоварвания. Въз основа на второто условие се определя максимално допустимата плътност [Nmax], µm, при която по правило няма пластични деформации. В някои случаи пресовите съединения могат да работят надеждно дори при наличие на пластични деформации в най-натоварената зона.
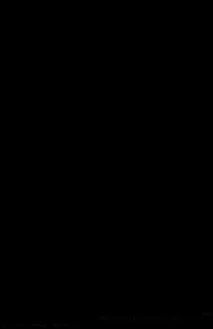
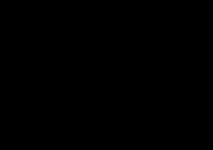
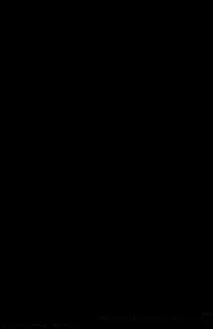
Фигура 1. Схема за изпълнение на намеса
1.2.1 Минималното специфично налягане върху контактната повърхност на вала и втулката [pmin], N/m 2, възникващо под въздействието на смущения, се определя по формулата:
[pmin]= ,
(1) |
(1) |
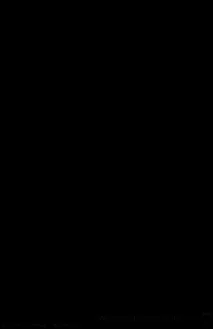
Мкр. - въртящ момент, N m;
- номинален диаметър на връзката, m;
l-контактна дължина, m;
f е коефициентът на триене при относително въртене на частите.
[pmin] = N/m 2 .
1.2.2 Най-малката проектна плътност, микрони се определя по формулата:
[pmin] dn
където E1 е модулът на еластичност на материала на вала, Pa;
E2 е модулът на еластичност на материала на втулката, Pa;
Коефициентите на Lame се изчисляват по следните формули:
където d1 и d2 са диаметрите съответно на вала и втулката, m;
μ1 и μ2 са коефициентите на Поасон съответно за материала на вала и материала на втулката.
µm.
1.2.3 Стойността на минимално допустимата плътност, микрони, се определя по формулата:
,
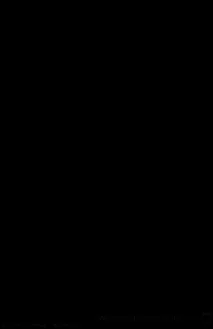
U е корекция, която отчита различните температури на средата по време на монтажа и работните температури на частите;
UC - корекция, отчитаща отслабването на херметичността под действието на центробежни сили;
UP - корекция, като се вземе предвид отслабването на стегнатостта при многократно натискане;
UR, дефиниран както следва:
където RzD, Rzd са грапавостта на повърхността съответно на втулката и вала, µm;
µm;
където α1, α2 - температурни коефициенти на линейно разширение на материала на вала и втулката, o C -1 ;
T1 и T2 - работни температури на вала и втулката, o C;
Тав. - температура на средата по време на монтажа на съединението, o C
µm;
µm.
1.2.4 Максимално допустимото специфично налягане [pmax], N / m 2 се определя по формулата:
р1= 0,58 σТ ,
р2= 0,58 σТ ,
където σТ и σТ са границата на провлачване на опън на материала на вала и втулката, Pa.
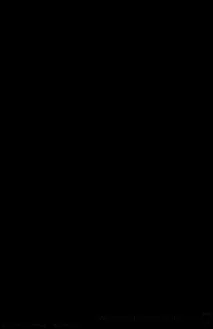
p2=0,58 280 10 6 =28,43 10 6 N/m 2 ;
Вземаме най-малката от двете стойности: [pmax] \u003d 28,43 10 6 N / m 2;
1.2.5 Максималната проектна плътност, µm, при която възниква [pmax], µm, се определя по формулата:
;
=
=28,43·106 ·0,198· =7,54 µm.
1.2.6 Максималната проектна плътност, микрони, като се вземат предвид корекциите, открити по-рано, се определя по формулата:
където е корекцията, като се вземе предвид увеличението на специфичното налягане в краищата на женската част, микрони.
=1,44 цт;
=0 цт;
=1 µm.
µm.
1.2.7 След като изберем системата от отвори и съответното качество (7 или 8), ние избираме стандартното прилягане съгласно GOST 25347-89.
Условия за кацане:
![]() |
Приемане на годни Ø32.