Рационализиране на 5S” опит в българското внедряване
Свързани статии
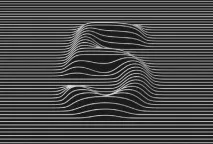
Валери Малцев, генерален директор на комбайновия завод Ростселмаш, Ростов на Дон
Дмитрий Мареновски, производствен директор на комбайновия завод Ростселмаш, Ростов на Дон
- Кой щадящ подход да изберете: европейски или източен
- Как да внедрим системата за рационализиране 5S в България
- Колко души трябва да бъдат включени в една работна група
- Какви конкурси ще помогнат за включване на персонала в прилагането на подобрения
- Какви загуби в дружеството в Очаково ще бъдат ликвидирани първо
Авторите на системата"Поръчка 5S" са японски производители. Въпреки това той абсорбира постиженията на световната индустрия, включително опита на СССР. Още през 20-те години на миналия век тук е разработена система за научна организация на труда, която включва всички постулати на съвременното „подреждане“. През 90-те години много от нейните постижения бяха загубени. Икономическите затруднения доведоха до проблеми със заплащането на персонала. Логичният резултат е напускането на високопрофесионални специалисти.
Комбайновият завод, от който започнахме да внедряваме lean производство, до идването на новото ръководство през 2000 г. се оказа точно в такава ситуация. За да го променим, започнахме да модернизираме производството. Част от цеховете бяха преоборудвани, пуснати бяха нови модели. Но скоро осъзнаха, че без участието на целия екип в процеса на усъвършенстване по-нататъшният напредък е невъзможен. Тогава решихме да внедрим системата "Поръчка 5S" в предприятието.
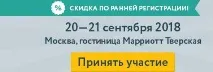
6 етапа на внедряване на системата "Организация 5S"
Етап 1. Избор на подход за внедряване на системата 5S
европейски подход. В предприятието е поканен професионалист, който изпълнява най-малко четири стъпки за внедряване на системата (почистване на ненужните, рационално поставяне на предмети на работното място, разработване на процедури за грижа за оборудването, изготвяне на стандарти). В този случай работниците на завода могат да поддържат само установена система. Подходът ви позволява бързо да се справите със задачата, но има два недостатъка: той е скъп и не гарантира устойчив резултат.
Източен подход. Това включва само обучение на персонала, тоест прилага се принципът „кажи същността и самият служител ще реши как да го направи“. Методът е трудоемък. Въпреки това знанията, придобити от служителите, са от голяма полза за тях, а крайният резултат е по-стабилен.
Предпочетохме методология с ориенталски подход на изпълнение.
Етап 2. Проучване на опита на други предприятия
Често мениджърът смята задачата за внедряване на системата за доста проста. Изглежда, какви трудности могат да бъдат причинени от почистването, поддръжката и настройката на оборудването от работниците? Достатъчно е само да се даде поръчка. Този подход обаче води до непредвидени разходи и съпротива на персонала. Затова отначало проучихме опита на десетки други предприятия. Бяхме готови да направим финансови инвестиции, за да подредим нещата и да работим в тясно сътрудничество с хората.
Фаза 3. Създаване на временна организационна структура и работни групи
Първоначално системата "Поръчка 5S" е внедрена в производствени цехове и сервизни отдели (ремонт, склад, транспорт).
За целта създадохме временна организационна структура. Основната структурна единица е работната група, която включва персонала на определена производствена област. За ръководители бяха назначени майстори. Ако броят на работниците на сайтанадхвърли 20 души, създаде две групи, най-уважаваният служител беше номиниран за ролята на лидер. В резултат на това бяха създадени 350 работни групи (всяка получи свой номер). Те трябваше да изпълняват редица функции:
- провеждайте редовни срещи за идентифициране на проблеми и намиране на решения;
- изготвя график за разгръщане на системата "Поръчка 5S" на базата на общ завод с разпределение на отговорностите в групата;
- изготвяне на информационен щанд, показващ актуалното състояние на нещата;
- своевременно да формира пакет от документи въз основа на резултатите от работата; например доклади „преди и след“, отразяващи динамиката на решаване на проблеми; правила за работа на служителите при откриване на повреди или дефектни части; графици за почистване на работните зони и др.
Етап 4. Обучение на персонала
Преди внедряването на системата внедрихме каскадно обучение. Първо го приеха ръководителите на работните групи. След успешното изпълнение на теоретичните и практическите задачи те проведоха занятия за своите подчинени. Процесът на обучение отне около три месеца. След това на общото събрание обявиха старта на проекта.
Етап 5. Включване на служители в процеса на подобряване
Внедряването на системата "Поръчване 5S" в разбирането на обикновения персонал е обичайна рутина. Затова в началото се стремяхме да събудим интерес у хората, да ги обединим в екип. Например, те оборудваха стаите, където се провеждаха срещите, не само с компютри и принтери, но и със сервизи за чай.
За да се поддържа положителното отношение на екипа към проектите, започнаха да се провеждат състезания: „Най-добър дизайн на щанда на работната група“, „Най-добър ръководител на работна група“, „Най-добра работна група“. Победителите бяха наградени с ценни награди, отразена беше дейността на водещите работни групикорпоративни медии.
Първоначално проектът се ръководи от директора по качеството. Например, при първоначалното почистване премахнахме 1000 тона метал (над 120 автомобила КамАЗ). Част беше изпратена за обработка на мястото за подготовка на партиди, част беше продадена. Но при преминаване към следващия етап (рационално разполагане на артикулите) темпът на изпълнение намаля, тъй като беше необходимо по-активно участие на ръководството. След това коригирахме отговорностите на участниците във временната организационна структура, започнахме да провеждаме конкурс за най-добро работно място и въведохме система от одити.
Етап 6. Преразпределение на задачите
След две години и половина степента на изпълнение отново спадна. Оказа се, че отделите за качествено обслужване и производство разбират принципите на прилагане на методологията по различен начин (за производствените работници основното е да завършат работата навреме). Разбрахме, че един човек не може да носи отговорност за проекта. С други думи, задачите трябва да се преразпределят във времето към онези звена, които са готови да ги решат по възможно най-добрия начин. На този етап директорът по операциите пое проекта и процесът тръгна от земята.
При преминаване към третия етап (почистване, проверка, отстраняване на неизправности) част от работата по оборудването беше поета от главния инженер. Това направи възможно внедряването на проекта TPM (Total Productive Maintenance), когато целият персонал е включен в процеса на подобряване.
Внедряваме системата 5S Organizing от 2006 г. Днес тя работи във всички подразделения, което направи възможно включването на 50% от персонала в решаването на проблеми. Системата за подаване на предложения спестява десетки милиони рубли годишно.
Например реализирали сме проекти, свързани с логистиката,ниво на качество. Освен това постигнатите резултати позволиха да се премине към следващия етап - внедряването на производствената система във всички предприятия на Rostselmash.
Експертно мнение
Виктор Кирилов, Експерт по подобряване на оперативната ефективност на предприятията, Москва; Доктор по икономика
Приходите на регионалното ресурсоснабдително предприятие се формират чрез заплащане на услуги (на фиксирана ставка) и инвестиции от градския бюджет.
През 2015 г. оперативните разходи започнаха да растат по-бързо от тарифите. Обемът на плащанията от потребителите се оказа по-нисък от планирания поради изпълнението на програмата за спестяване на ресурси. Освен това градът намали размера на субсидиите.
Беше необходимо спешно да се промени финансовият модел на предприятието. Ръководството имаше избор:
- ограничаване на инвестиционните програми, намаляване на броя на персонала с 22%;
- повишаване на производителността на труда и намаляване на времето за изпълнение на инвестиционните проекти.
Предпочитанието беше дадено на втория вариант.
Търсене на загубено работно време. Анализира работния ден на всеки екип. Оказа се, че всички бригади направиха всичко. Имаше ситуации, когато екип беше изпратен на важна работа, която не беше най-ефективната. Освен това мениджърите могат да изпратят на работа екип от пет-шест души, за които са достатъчни трима души. Това доведе до прекъсване на оборудването. Обедните почивки можеха да отнемат до два часа поради трудния транспорт до столовата и обратно.
За да намерим оптималното решение, организирахме интервюта и фокус групи с участието на ръководството. Оказа се, че служителите нямат мотивация да работят бързо. Мнозина се придържаха към принципа "войникът спи - службата продължава". Те не саботираха работата, а инициативатане бързаха да се появят.
Решение 2. Система за оценка на екипажа. Одобрени стандарти за извършване на операции. Въведохме система за оценка на бригадите: за всяко действие те получават определен бал. Особено внимателно се анализира работата с използването на специално оборудване. Оценката се извършва веднъж седмично, а окончателното сравнение се основава на резултатите от месеца. Изчислен е средният брой точки на смяна. Следва класирането на бригадите. Най-добрите (лидерите) бяха изпратени на работа със специално оборудване. Разпределен е и на други бригади, но на остатъчния принцип. Колкото по-високо е мястото в класацията, толкова по-големи са шансовете да получите този вид работа. Тази мярка позволи да се увеличи производството на екипи средно с 18%. В допълнение, рейтингът постави началото на негласна конкуренция както в отделите, така и на ниво предприятие.
Решение 3: Организиране на допълнителни заведения за хранене. През следващите шест до осем месеца ръководството обмисля възможността за организиране на допълнителни заведения за хранене. Това трябва да намали продължителността на вътрешносменните движения на екипажа и да намали загубата на работно време с 10% (40–60 минути).
Говори генералният мениджър
Юрий Антонов, генерален директор на предприятието Очаково, Москва
Внедряваме системата за щадящо производство от 2010 г. В него всичко, което не добавя стойност към продукта, се счита за отпадък. Особено внимание се обръща на скритите загуби. Именно тяхната идентификация ни създаде трудности. Беше необходимо да се разбере как да се цифровизират загубите, така че по-късно да бъде възможно да се оцени ефектът от тяхното елиминиране.
Пример за оценка на загубата. В офиса няма копирна машина. За да направите копия, трябва да отидете на друг етаж. Обиколката отнема осем минути. За да оцените загубата, трябва да изчислите средния брой пътувания на служител на ден, умножете по брояработни дни на месец и на стойност един работен час. Времето за копиране не е необходимо да се брои. Ако периодът на изплащане на оборудването е кратък (около година), тогава си струва да закупите копирна машина.
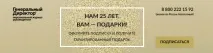
Валери Малцев завършва MAI. От 1993 г. работи на ръководни длъжности в предприятията на индустриалния съюз "Нова общност" ("Нов сапунен котел", "Авиастар-СП"). От 2003 г. - генерален директор на предприятието Rostselmash.
Дмитрий Мареновски завършва Донския държавен технически университет. От 2000 г. работи в комбайновия завод Ростселмаш. През 2010 г. той става директор по качеството, на настоящата си позиция от 2013 г.
Combine Plant Rostselmash LLC Сфера на дейност: производство на селскостопанска техника (Combine Plant Rostselmash LLC е част от групата компании Rostselmash) Територия: централен офис в Ростов на Дон, производствени обекти в Казахстан, Канада, САЩ Заетост: повече от 10 хиляди. Основни марки: Rost selmash, Versatile Приходи: 31,8 милиарда рубли
Виктор Кирилов - член на асоциацията на BPM-професионалистите (англ. Business Process Management - управление на бизнес процеси), преподавател в Санкт Петербургския държавен технологичен университет за растителни полимери и Московския държавен университет. М.А. Шолохов. Реализирани проекти за изпълнение на програми за повишаване на производителността на труда, намаляване на производствените загуби. Автор на повече от 30 публикации по тази тема.
ЗАО МПБК „Очаково”Сфера на дейност: производство на бира, квас, сокове, медовини, безалкохолни и слабоалкохолни напитки, питейна и минерална вода, вино, водкаТеритория: централен офис в Москва, заводи в Москва, Краснодар, Пенза и Тюмен Брой персонал: 5000 годишен обем на емисия: 260 милиона.декалитри напитки